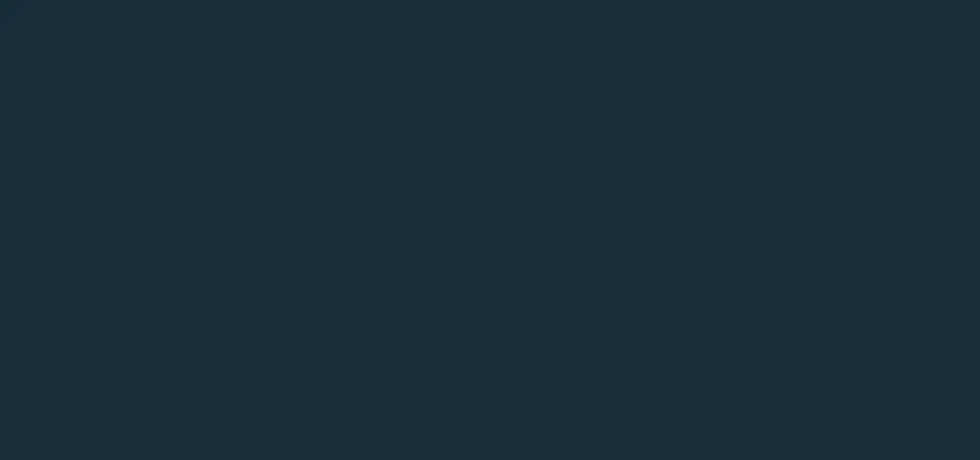.webp)
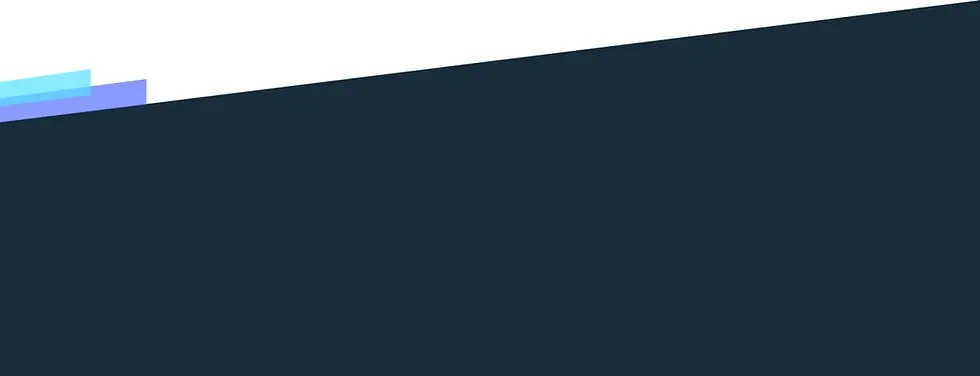.webp)
Challenges Addressed
Fragmented Data Sources:
The manufacturer’s existing systems were siloed, making it difficult to collect and analyze data from different production lines. This fragmentation resulted in delays in decision-making and poor resource management.
Limited Real-Time Insights:
Without a centralized monitoring solution, the manufacturer lacked real-time visibility into the performance of its production operations. This made it challenging to identify bottlenecks quickly and take corrective actions to optimize processes.
High Maintenance Costs:
Relying on multiple on-premises monitoring systems led to elevated maintenance costs and the heavy use of IT resources. This, in turn, diverted focus from the company’s core manufacturing activities.
Inflexible Reporting:
The manufacturer’s existing reporting tools were inefficient and rigid, offering limited customization options. This made it difficult to generate reports and insights that addressed specific operational needs.
NEXA's Approach
NEXA developed a scalable, cloud-based platform that seamlessly integrated with the manufacturer’s existing automation systems, providing real-time monitoring and analytics to improve data accessibility and informed decision-making while significantly reducing maintenance costs. This platform consolidated data from various production lines, sensors, and machines into a single system for easier access and analysis. With real-time visibility, the solution enabled the client to monitor production metrics, equipment status, and operational performance, enhancing overall operational efficiency.


Cloud-Based Platform for Industrial Automation Monitoring
Client Spotlight
A prominent manufacturer in the industrial sector faced significant challenges in monitoring and controlling its extensive automation processes. With numerous production lines running simultaneously, the company required a solution to consolidate data from various sources and provide real-time visibility into operational performance. They approached NEXA to design a cloud-based platform that could enhance their monitoring capabilities, optimize resource allocation, and streamline operational efficiency.
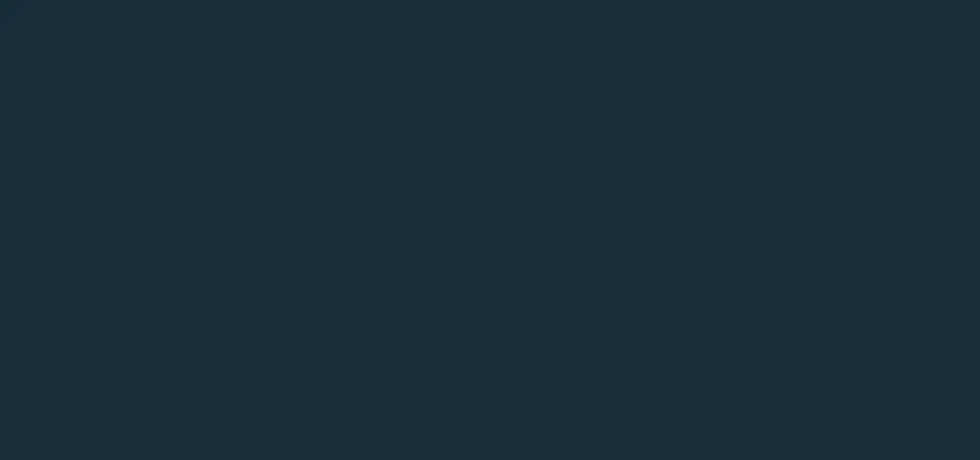.webp)
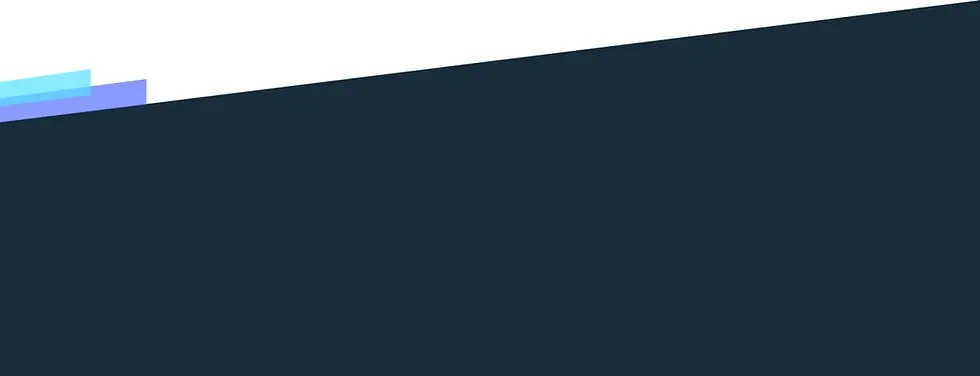.webp)
Results Achieved
Operational Visibility: The cloud-based platform provided the client with real-time insights into production processes, resulting in a 50% reduction in downtime due to proactive monitoring and quicker identification of issues.
Streamlined Decision-Making: With consolidated data accessible in real-time, the manufacturer was able to make faster, more informed decisions, significantly improving their ability to address operational challenges.
Cost Savings: The transition to a cloud-based solution yielded substantial cost savings for the manufacturer, with a notable 30% reduction in maintenance costs. Before this shift, the company was burdened with the financial and operational overhead associated with maintaining multiple on-premises systems.
Customizable Reporting: The platform’s flexible reporting capabilities enabled tailored insights, empowering the management team to focus on performance metrics relevant to their specific operational goals.
Increased Employee Engagement: Employees reported increased satisfaction due to reduced manual reporting tasks and improved access to real-time information. This led to a more proactive and engaged workforce focused on optimizing production.
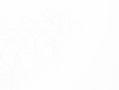
Implementation
Requirements Gathering: NEXA's team engaged in detailed consultations with stakeholders from both the manufacturing and IT departments to identify critical pain points and define the client’s monitoring requirements.
User Interface Development: NEXA prioritized the development of a user-friendly dashboard to enhance the usability and effectiveness of the cloud-based platform. This dashboard was designed with a focus on intuitive navigation, ensuring that users from various backgrounds—whether they were production managers, quality control staff, or IT personnel—could easily access and interpret the information they needed.
Testing and Optimization:
The platform underwent rigorous testing in various operational scenarios to ensure its reliability and effectiveness. Feedback from the client’s staff was incorporated to enhance usability.
Deployment and Training:
Following successful testing, the platform was deployed across the client’s manufacturing facility. NEXA provided comprehensive training to staff, ensuring they could effectively utilize the platform’s features.