AI in Industrial Automation: Leveraging Machine Learning for Predictive Maintenance
- NEXA
- Nov 9, 2024
- 3 min read
Updated: Nov 11, 2024
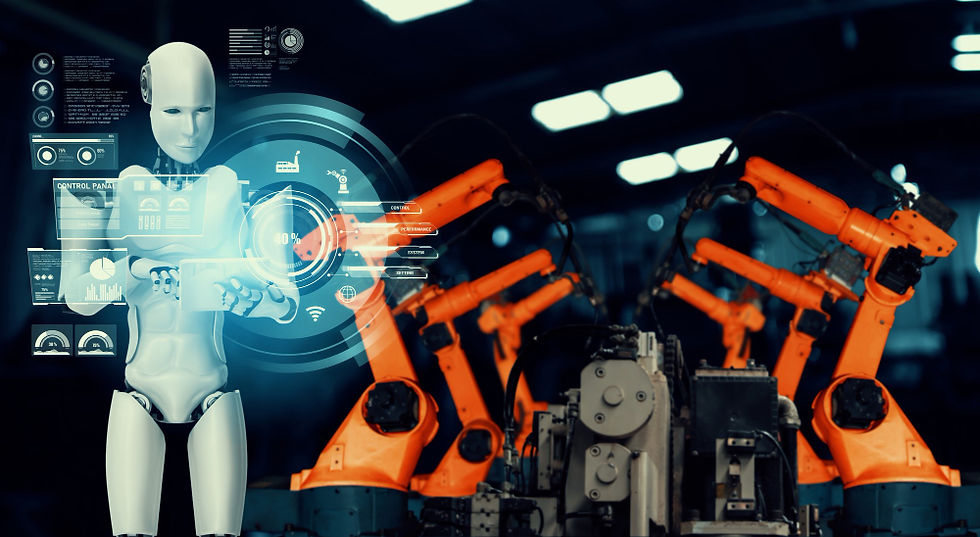
The integration of industrial automation with advanced technological systems is reshaping business operations, offering transformative ways to optimize processes. Predictive maintenance exemplifies this evolution by enhancing operational efficiency and minimizing downtime. Through sophisticated data-driven insights, it allows businesses to predict equipment failures before they happen, reducing costs and boosting overall productivity.
Understanding Predictive Maintenance
Predictive maintenance (PdM) refers to a strategy that uses data analysis tools and techniques to predict when equipment or machinery will require maintenance. Unlike traditional maintenance practices, which often rely on scheduled or reactive approaches, predictive maintenance focuses on the actual condition of assets. Through the collection and analysis of data from sensors embedded within machinery, predictive maintenance allows industrial organizations to perform repairs only when necessary.
Role of AI and Machine Learning in Predictive Maintenance
Predictive maintenance is revolutionizing industrial operations by enabling businesses to predict equipment needs based on data-driven insights. This approach moves beyond traditional maintenance strategies, focusing on anticipating equipment that requires service, thereby preventing costly downtimes and enhancing overall productivity.
In industrial settings, predictive maintenance relies on data analysis to monitor temperature, pressure, vibration, and operational parameters. Systems can predict equipment malfunctions or necessary maintenance by identifying patterns from this historical and real-time data.
Techniques Used in Predictive Maintenance
Supervised Learning Techniques: Supervised learning utilizes historical data with known outcomes to train models that can forecast maintenance needs. These models predict future equipment performance based on past occurrences, including prior maintenance or detected faults. Popular algorithms used include decision trees, random forests, and support vector machines.
Unsupervised Learning for Anomaly Detection: Unlike supervised methods, unsupervised learning identifies hidden patterns without labeled data. It excels at detecting anomalies in machine behavior and spotting deviations from standard operational conditions. Techniques such as clustering, K-means, and principal component analysis (PCA) are commonly applied.
Reinforcement-Based Approaches: Reinforcement strategies enable models to make decisions through iterative feedback. These approaches optimize maintenance schedules based on system performance data, enhancing operational decision-making and overall system efficiency over time.
Deep Learning Applications: Deep learning employs multi-layered neural networks capable of extracting insights from extensive datasets. This is particularly advantageous in environments with complex systems where traditional models may struggle. Deep learning can automate feature extraction, making it ideal for tasks like diagnosing faults and predicting failures.
Benefits of Data-Driven Predictive Maintenance
Minimized Downtime: Predictive maintenance reduces unplanned downtime by enabling proactive scheduling of maintenance tasks. This prevents operational disruptions and ensures machinery remains functional for longer periods.
Cost Reduction: By addressing issues before they escalate, businesses minimize repair costs and extend the lifespan of their assets. Early detection prevents major breakdowns and reduces the need for expensive part replacements.
Enhanced Asset Performance: Advanced models continuously monitor asset health, optimizing their operation and leading to improved productivity, superior output quality, and better energy and resource utilization.
Safety Improvements: Early detection of potential hazards, such as overheating or abnormal pressure levels, helps prevent accidents and creates a safer workplace environment.
Optimized Resource Use: Predictive maintenance ensures resources, including personnel and spare parts, are allocated only when necessary. This efficient resource management leads to better planning and minimized waste.
Challenges in Implementing Predictive Maintenance Solutions
Data Quality and Availability: Reliable predictions depend on high-quality data from sensors and machinery. Data gaps or inaccuracies can reduce the effectiveness of predictive systems.
Integration with Existing Systems: Many facilities rely on legacy systems. Integrating predictive maintenance capabilities often requires complex upgrades and significant investments.
Skill Requirements: Successfully implementing predictive maintenance demands expertise in data science, automation, and system integration—a lack of such skills may hinder adoption.
Initial Costs: Implementing predictive maintenance requires a notable upfront investment, covering new sensors, equipment upgrades, and personnel training. While the long-term benefits can offset these costs, they may pose a barrier to smaller organizations.
Applications Across Industries
Manufacturing: Predictive maintenance helps identify and address issues in machines like conveyor belts, robotic arms, and CNC machinery. Early detection prevents production delays and optimizes factory output.
Aerospace: Aircraft safety and reliability depend heavily on predictive maintenance, with real-time monitoring of engines and avionics systems to forecast potential malfunctions.
Energy: Energy providers use predictive strategies to monitor critical infrastructure such as turbines and transformers, ensuring consistent service and reducing repair costs.
Automotive: Fleet performance monitoring through predictive maintenance allows for timely interventions, reducing downtime and boosting efficiency.
Predictive Maintenance: Paving the Way for Cost Savings and Operational Resilience
Predictive maintenance is becoming integral to industrial operations, offering cost savings, increased safety, and optimized performance. While challenges such as integration and data quality persist, businesses stand to gain significant long-term advantages. By embracing data-driven predictive strategies, companies ensure their operations are resilient, efficient, and well-prepared for future demands.
コメント